Writing Validation Protocols for Medical Devices
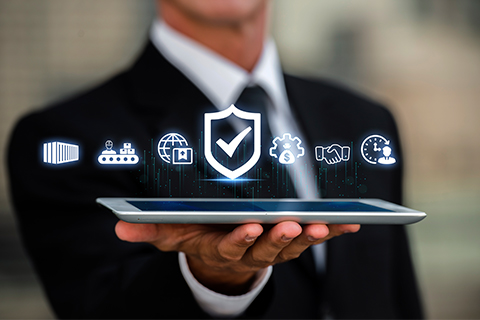
Validation protocol is defined as a documented plan for testing a medical device to confirm that the production process used to manufacture the product meets the specific user, technical, and Regulatory requirements. This includes a review of process variables and operational limitations and the analysis of test results under actual use conditions.
The validation process involves several tangible actions. The steps are elucidated as follows: